Civil Engineering
Social infrastructure – what we can build, how we build it and how long it lasts – makes our society possible, and beyond that, makes it enduring and inspiring. Scarcity Zero can revolutionize our recently-neglected social infrastructure to great social benefit by allowing public works projects to complete faster, less expensively and on larger scales.
You’ll recall that repairing the decaying infrastructure across our nation is expected to cost several trillions of dollars with today’s tools and methods – even in the most conservative estimates.[2] These are repairs that need to be made, yet we have neither the earmarked funds nor the political willpower to pay for them. However, as with energy and resources, technology provides an opportunity to solve the problem for us by leapfrogging limitations cost-effectively.
How exactly? First, let’s cover some givens:
Most heavy machinery today is powered by diesel, which makes fuel a considerable expense of any construction project.[3] And while diesel engines have legendary reliability, the pumps, belts, and hydraulics in heavy machinery aren’t generally as dependable, which leads to delays and additional costs when they eventually fail. Electric construction equipment on the other hand is mechanically simpler, and as such can avoid many of these complications while delivering the same standard of performance as their diesel counterparts.[4] As prices for electricity drop with the implementation of Scarcity Zero, fuel becomes less of a construction expense (all the more so once hydrogen becomes a more viable industrial fuel).
Building materials also command significant percentages of construction budgets.[5] With Scarcity Zero, construction projects could source better materials for lower prices. This would enable us to build lighter and stronger structures with less expense than we can today; and as a structure’s maximum size is limited largely by strength-to-weight ratios, these materials would also increase the scale of what we are capable of building.
Once computer modelling, 3D printing, and factory prefabrication are added in, however, is when we truly start building the future. These technologies have been around for only the past decade, meaning that the majority of structures in our society were built without the aid of computers, and anything built before the late 1970s didn’t even involve a calculator. Today, architectural software allows us to design structures virtually on computers. This provides engineers with 3D representations of what they’re constructing along with highly accurate predictions of material requirements and limits of load and scale. The following images, for example, respectively show a bridge being designed on a computer and another being 3D printed in real time:
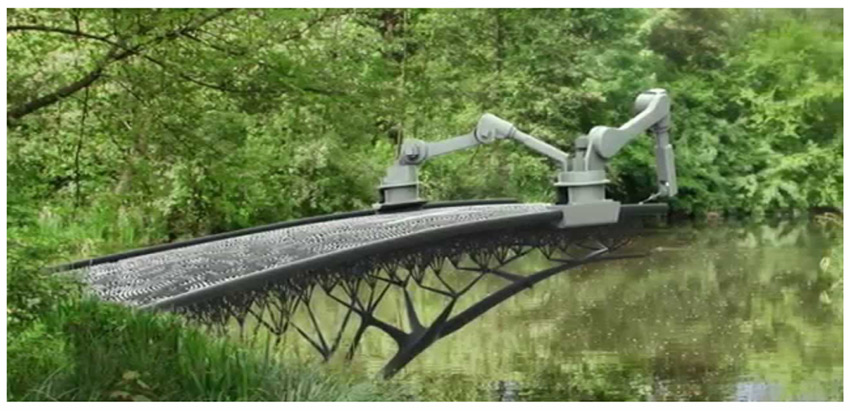
Considering that many of these technologies are in their infancy with regards to civil infrastructure, there is ample room for them to grow in the future. Integrating improvements in material science, nigh-unlimited energy and resources, and design-first principles of standardization and modularity only stand to serve as accelerants. We previously saw how we can embrace these advances to build houses, buildings and prefabricated systems, but this concept applies to the manufacture of practically anything on a large scale.
If we can prefabricate jetliners and LFTRs, why not bridges, tunnels, apartment buildings, and skyscrapers? Aerospace-grade engineering carries the highest requirements for reliability in the world, and today we already can completely assemble a flagship jetliner every nine business days – or 3D print sophisticated components for the same in a matter of hours. A world powered by Scarcity Zero grants us the means to raise the bar higher still.
Within civil engineering, examples include:
Next-generation roads, bridges and tunnels. Railroads and paved highway networks rank among the greatest marvels of human engineering, revolutionizing travel, transportation and commerce on global scales.
Yet in many ways, such infrastructure is only as useful as its ability to overcome obstacles in the landscape, something made possible through bridges and tunnels – engineering accomplishments that we don’t often think about when impressive structures come to mind. And yet:
- While not the longest bridge in the United States, at 4.8 miles the Chesapeake Bay Bridge is one of the most important, as it connects Delaware and Maryland’s Eastern Shore with the Baltimore-Washington Metropolitan Area. Roughly 25.6 million vehicles travel on it every year, each one saving time and fuel that would be devoted to longer routes should the bridge not exist.[6]
How much time and fuel? Assuming each of these 25.6 million vehicles traveled between Washington, DC and Dover, Delaware, they need drive only 93 miles for 1.8 hours if they use the bridge. If not, they would need to drive 134 miles for 2.75 hours via I-95.[7] This means that over the past 10 years, assuming consistent traffic and 21 miles per gallon fuel economy, the Chesapeake Bay Bridge has collectively saved motorists a total of one billion miles of driving distance, 224.3 million hours (2,776 years) of driving time, and roughly 500 million gallons of fuel.
- The Colorado I-70 corridor splits the Rocky Mountains with a highway, allowing motorists to avoid slow and often precarious mountain passes. The corridor is made possible through the 1.7-mile-long Eisenhower-Johnson tunnel, which was completed in 1979. It takes approximately four hours on I-70 to travel the 235 miles from Denver to Grand Junction on opposite sides of the Continental Divide. Without the corridor, it would take approximately 8.6 hours to travel the 432 miles via U.S. Route 40.[9]
To put those numbers in perspective, the highway and tunnel has saved each vehicle 4.6 hours of driving time and a driving distance of 197 miles. As roughly 13 million vehicles travel through the tunnel annually,[10] we’ll conservatively assume that from 1979 to 2018 a total of 400 million vehicles have traveled this route to Grand Junction. At an assumed average fuel economy of 21 miles per gallon, this tunnel system has collectively saved drivers 79 billion miles of driving distance, 1.8 billion hours (210,000 years) of driving time, and 3.7 billion gallons of fuel.
Under those assumptions, these two public works projects, alone, have collectively saved motorists a total of 80 billion miles of driving distance, 213,000 years of driving time, and 4.2 billion gallons of fuel.
Both the Chesapeake Bay Bridge and the Colorado I-70 corridor were built with technology from the 1950s-1980s – a far cry from what we have available today, which in itself is a far cry from the capabilities we would have with Scarcity Zero. Under the framework, we would be able to increase the scale of our bridges and tunnels – connecting places in ways that were never before possible.
Megabridges: as the name suggests, a megabridge is a bridge of large size and scale. Built with the strongest materials available, a megabridge spans longer distances and support more lanes and thus heavier loads. They can also enable travel of both road and rail, increasing diversity of use and overall social utility.
Megabridges have already made their debut on the world stage. The above concept images respectively show the proposed Fehmarn Belt Fixed Link,[11] connecting Germany and Denmark, and the Sheikh Rashid bin Saeed Crossing megabridge in Dubai.[12] The image below shows the recently completed Zhuhai-Macau Megabridge connecting mainland China to the island of Macau:
As impressive as they are, neither of these projects can yet utilize large-scale factory prefabrication or next-generation synthetics, meaning they are ultimately constructed ad-hoc with less advanced material options than would be possible with Scarcity Zero. Future megabridges can avoid these constraints. Imagine if construction crews didn’t need to pour concrete, lay cable, steamroll asphalt or spot-weld junctions by hand, each and every time? What if they instead could take prefabricated pylons, platforms, support arches, and integrated renewables, assembling the entire bridge like a hobby kit, just on a larger scale?
This approach is not only possible, it can be a hallmark of tomorrow’s manufacturing capabilities. Such an approach further allows architects to expand their vision, as it reduces several of the problems with modern construction and material sciences. As civil engineers can hash out the technical details of a bridge with ever-more sophisticated software at the design stage, it could be rapidly determined what it would take to enlarge the bridge to greater scales of size, should the materials and manufacturing methods be present. Such efforts could lead to a day where bridges eight to twelve lanes wide with lengths upwards of 100 miles or more enter the realm of possibility. That is the future made possible by effectively unlimited energy and resources.
Megatunnels: the megatunnel is the evolution of subterranean / underwater transportation structures. Of the megatunnels in existence or in planning stages today, perhaps the best examples are the 30-mile Channel rail tunnel connecting England to France, the 33-mile Seikan tunnel connecting the Japanese islands of Honshu and Hokkaido, and the 35-mile Gotthard Base Tunnel under the Alps.[13]
These tunnels are rightfully considered among mankind’s most impressive accomplishments. But challenges remain to increasing their scale, especially in the context of submerged tunnels. There are unique complications to building submerged tunnels that are not present with bridges, namely the presence of extreme water pressure.
Building a submerged tunnel between England and France, for instance, is possible today, as the depth of the English Channel doesn’t exceed 150 feet.[14] Yet building a submerged tunnel from, say, Tokyo to Beijing, or London to New York, is far more difficult. When water depths reach thousands of feet, pressures are so great that hardened steel structures can crumple like paper bags. The material advances made possible by Scarcity Zero allow us to significantly extend our capabilities to build structures that can withstand such pressures. They also allow us to reach an even more achievable goal of floating megatunnels that would serve the same effect as deep water variants in function.
Through a combination of buoyancy control mechanisms or cables/weights tethering the tunnels to the ocean floor, these tunnels would stay close to above-water atmospheric pressures to avoid complications with structural integrity or surface breaches in the case of emergencies:[15]
Two concepts shown below:
As a structure’s weight displacement is different when submerged as opposed to on land, the buoyancy of these tunnels can be calibrated to maintain high degrees of stability, strong enough to support vehicle and even high-speed rail travel. Norway is already considering building submerged tunnels to cross fjords, a model that could be applied to more ambitious projects over larger bodies of water as our technology improved.[16] Scarcity Zero-underwritten energy cost and material advancements bring this possibility closer to reality.